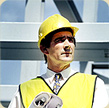
Market Leaders was the counsulting for coring and wire sawing concrete base of king Ramses project
The statue was discovered in 1820 by Giovanni Battista Caviglia at the Great Temple of Ptah of Mit Rahina, near Memphis, Egypt. King
Ramses II ruled Egypt for 67 years during the 19th Dynasty (1279-1212 BC). The statue measures approximately 67 feet in height and weighs
approximately 85 tons.
Following the Egyptian revolution of 1952, President Nasser requested the statue be moved from Mit Rahina to Bab El Hadid
Square, the main railway station square in Cairo, in 1956. The statue was transported to its new location, which was renamed Ramses Square,
and is one of the most famous statues of the Egyptian pharaohs. Since this time, the square has undergone significant development including
the construction of waterfalls and colored lighting around the statue, together with the building of road infrastructure and bridges around
the square in the 1980s. Unfortunately, all this has led to Ramses Square incurring increased noise, pollution and high vibration levels.
In 2005, the Egyptian Ministry of Culture, afraid the statue may be damaged by the constant vibrations and environmental conditions in
the square, took the decision to relocate the statue approximately 30 miles away to the Pyramids close to Giza City. By early 2006, the project
was announced and tendered internationally. The winning bid was submitted by Arab Contractors Co. (Public Egyptian Contractors Co.),
who approached several European companies to provide their ideas on how to dismantle and move the statue. Three ideas were presented. The
Arab contractors asked Dr. Ahmed Hussein of the Engineering Faculty of Ain Shams University to submit a risk analysis. He found that the
three ideas provided were too risky, and so came up with a completely different one. Arab Contractors were pleased with this new concept,
Did You Know? Pyramids
During the earliest period of the 3rd and 4th dynasties, pyramids were constructed wholly of stone. Locallyquarried limestone was the material of choice for the main body of these pyramids, while a higher quality of limestone quarried at Tura, near modern Cairo, was used as the outer casing. Granite, quarried near Aswan, was used to construct some architectural elements, including the porticullis and the roofs and walls of the burial chamber. Occasionally, granite was used in the outer casing as well. In the early pyramids, the layers of stone forming the pyramid body were laid sloping inwards. However, this configuration was found to be less stable than simply stacking the stones horizontally on top of each other, One of the major problems faced by the early pyramid builders was the need to move huge quantities of rock. Some illustrations show 172 men pulling an alabaster statue of a pharaoh on a sledge. The statue is estimated to weigh 60 tons and it is estimated that 45 workers would be required to start moving a 16,300-kilogram lubricated block, or eight workers to move a 2,750-kilogram block. Many archaeologists surmise that it took tens of thousands of skilled workers to build the pyramids, particularly the Great Pyramid of Giza. These workers camped near to the site and would work for a salary or as a form of tax payment (levee) until the construction was completed. As the stones forming the core of the pyramids were roughly cut, especially in the Great Pyramid of Giza, the material used to fill the gaps was a problem. Huge quantities of gypsum and rubble were needed. The filling has almost no binding properties, but was necessary to stabilize the construction. To make the gypsum mortar, it had to be dehydrated by heating, and this required a lot of wood. Some findings suggest that Egypt had to strip its forest and scrap every bit of wood it had to build the pyramids of Giza. Workmen probably used copper chisels, drills and saws to cut softer stone, such as most of the limestone. The harder stones, such as granite, granodiorite, syenite, and basalt could not be cut with copper tools alone. Instead workers used time consuming methods like pounding with dolerite, drilling and sawing with the aid of an abrasive, like quartzite sand. Blocks were transported by sledge likely lubricated by water. Leveling the foundation was accomplished by use of water-filled trenches.
and contracted Dr. Hussein to complete the design, follow-up steps and transportation requirements. Hussein created a special design that allowed the statue to be transported in its standing position. Mohamed Labib of CSDA member Market Leaders was the consulting engineer for the core drilling and wire sawing of the statue’s concrete base which was a major part of the planned project. Market Leaders began testing the concrete using several core-drilled test holes and wall and wire sawed cuts in various locations, away from the main base of the statue. The main concrete base under the statue measured approximately 16 feet in length, seven feet in width and stood 13 feet high. In addition, radar scanning and vibration sensing equipment, including 27 sensors around the statue’s base, was fitted. This equipment was monitored for two weeks prior to work commencing to record the live vibrations of the statue and to ensure all cutting work did not exceed typical street vibration levels. Two hydraulic systems were employed to cage the statue, consisting of four hydraulic cylinders, mounted on the four corners of the statue with a supporting steed structure. Another four supports for the basket carried the part of the concrete base located underneath the statue. A one-inch-thick steel plate was placed around the concrete base, using one-inch-diameter core holes and threaded steel bars to hold this part of the concrete base in one piece. The base was then injected with high-strength concrete to make this part of the base more robust. Seven 10-inch-diameter holes were created below the steel plate,
The project was a great success, and Mohamed Labib was pleased to have been a part of it. "It was a great opportunity to be the consulting engineer for the coring, floor, wall and wire sawing of such a large and prestigious job. Market Leaders is very proud to have played an important role in this project."